Cleaning Checklist for Wood Businesses
You should clear sawdust daily using industrial vacuums and wipe down tools to prevent buildup. Weekly, deep clean machinery parts, lubricate moving components, and sanitize surfaces. Use HEPA-filter vacuums and dust extraction systems to manage fine particles. Regularly maintain tools by oiling blades and cleaning vents. Sort wood waste into labeled bins and partner with recyclers. Keep humidity stable and guarantee good airflow to protect materials and health. Proper routine care boosts safety and efficiency—explore further to master these essential steps.
Daily Cleaning Tasks for Wood Shops
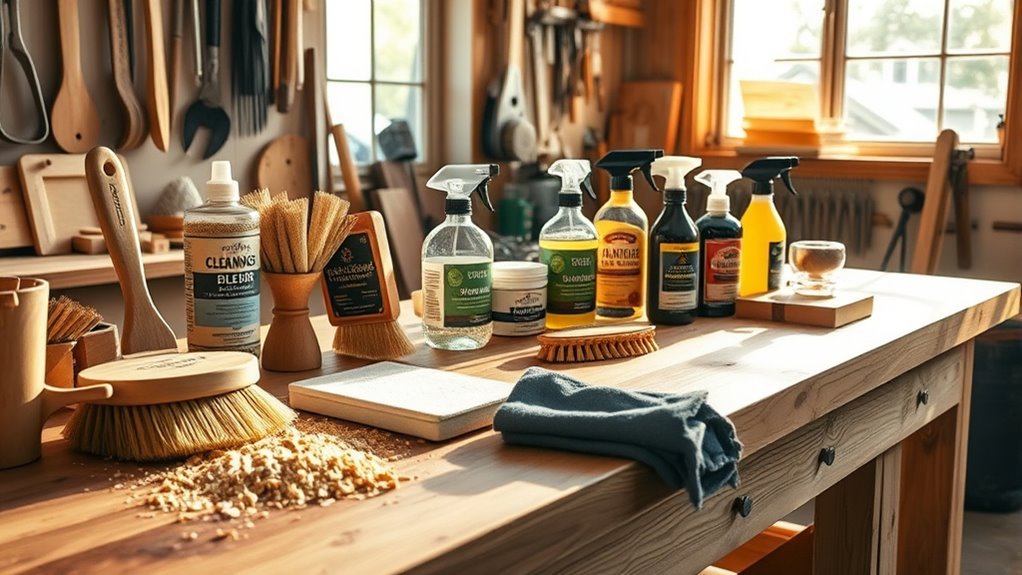
Although it might seem tedious, daily cleaning in wood shops is essential to maintain safety and efficiency. You must follow strict safety protocols to prevent accidents and guarantee a smooth workflow. Start by clearing sawdust and wood chips from all work surfaces and floors using appropriate cleaning supplies, such as industrial vacuums and brushes. Wipe down machinery and tools to remove residues that can impair their function or cause hazards. Empty trash bins regularly to avoid clutter and fire risks. Inspect ventilation systems daily to guarantee dust extraction operates properly, reducing airborne particles. By dedicating a few minutes each day to these tasks, you protect both your workspace and your freedom to work efficiently without interruptions caused by preventable hazards. Consistency here is non-negotiable for a safe, productive environment.
Weekly Deep Cleaning Procedures
Daily cleaning keeps your wood shop running safely, but weekly deep cleaning takes maintenance a step further to confirm long-term efficiency and safety. Scheduling deep cleaning on a consistent basis guarantees you tackle hidden grime, grease build-up, and neglected corners that daily tasks miss. Focus on disassembling and thoroughly cleaning machinery parts, inspecting and lubricating moving components, and sanitizing work surfaces. Pay close attention to storage areas and walkways to prevent hazards. Set a clear cleaning frequency—once a week is ideal—to prevent dirt accumulation that compromises equipment performance and your workspace’s safety. By adhering strictly to this schedule, you maintain operational freedom, reduce unexpected downtime, and extend your tools’ lifespan. Weekly deep cleaning isn’t optional; it’s essential for a productive, safe wood business.
Proper Dust and Debris Removal Techniques
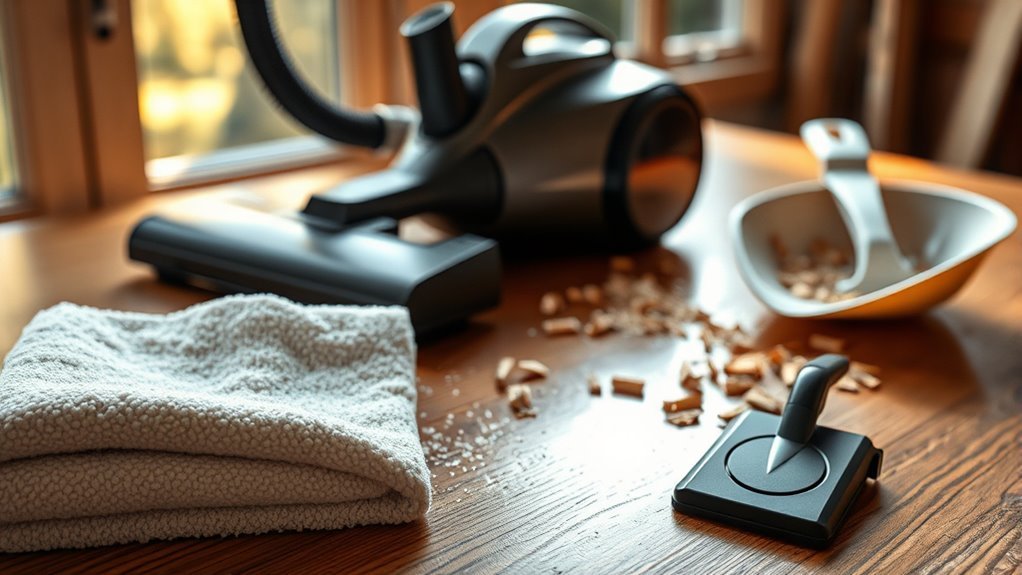
When handling wood, dust and debris accumulate quickly and can create serious hazards if not managed properly. Effective dust management and debris containment are essential to maintain a safe, clean workspace and guarantee your freedom from health risks and operational delays. Here’s how you can master proper dust and debris removal techniques:
- Use industrial vacuums with HEPA filters to capture fine dust particles at the source.
- Employ dust extraction systems connected directly to your woodworking machines.
- Regularly sweep and mop floors to prevent dust buildup and keep debris contained.
- Implement containment zones using barriers or mats to restrict debris spread.
Maintaining and Cleaning Woodworking Tools
Since your woodworking tools endure constant wear and exposure to dust and resin, maintaining and cleaning them regularly is essential to guarantee their accuracy, safety, and longevity. Focus on thorough tool maintenance to prevent rust and buildup that compromise performance. Use appropriate cleaners and lubricants after each use, inspect blades and joints for damage, and store tools in dry, organized spaces.
Tool Type | Cleaning Method | Rust Prevention Tip |
---|---|---|
Hand Saws | Wipe with cloth, oil blade | Apply light machine oil |
Chisels | Remove resin, sharpen | Store in dry cabinet |
Power Tools | Blow out dust, clean vents | Use rust inhibitor spray |
Planes | Clean sole, oil moving parts | Keep in sealed case |
Measuring Tools | Wipe clean, avoid moisture | Store in protective case |
Consistent maintenance guarantees your tools remain reliable and safe, empowering your woodworking freedom.
Managing Waste and Recycling Wood Scraps

Although managing waste might seem like a secondary task, properly handling wood scraps is essential for both environmental responsibility and workshop efficiency. You need to implement strict waste segregation to separate recyclable materials from general waste. Embracing recycling initiatives reduces landfill impact and recovers valuable resources. Here’s what you should focus on:
- Set up clearly labeled bins for different wood types and contaminants.
- Regularly collect and store wood scraps to prevent clutter and hazards.
- Partner with local recycling centers that accept wood waste.
- Educate your team on the importance of waste segregation and recycling initiatives.
Cleaning Safety Equipment and Workstations
Because safety equipment and workstations endure constant use, you’ve got to clean them thoroughly to maintain their effectiveness and secure a safe workspace. Start by inspecting your safety gear—helmets, gloves, and goggles—for dust, debris, and damage. Use appropriate cleaning agents and dry them completely before reuse to prevent contamination or malfunction. Next, focus on your workstation layout: clear sawdust and wood chips regularly to avoid slip hazards and guarantee tools are accessible and organized. Wipe down surfaces with a damp cloth and suitable cleaner to remove buildup without damaging materials. Maintaining a clean, orderly workstation layout not only boosts productivity but also minimizes risks. By prioritizing the cleaning of safety gear and workstations, you protect yourself and your team, preserving the freedom to work confidently and efficiently.
Handling and Cleaning Oil and Adhesive Residues
Tackle oil and adhesive residues promptly to prevent buildup that can impair equipment function and compromise product quality. You’ll want to master effective oil absorption techniques and adhesive removal methods to maintain a smooth operation.
- Use absorbent pads or powders immediately on oil spills to minimize spread.
- Apply industrial-grade solvents designed for adhesive removal, ensuring they’re safe for your surfaces.
- Scrape off excess adhesive gently with plastic tools to avoid surface damage.
- Follow up with a thorough wipe-down using a degreaser to remove residual oils and adhesives.
Organizing Storage Areas for Materials and Supplies
When you organize your storage areas efficiently, you’ll reduce retrieval times and minimize damage to materials. Start by evaluating your current layout and implementing tailored storage solutions that maximize space and accessibility. Use clear labeling and designated zones for different material types to streamline material organization. Vertical shelving and modular bins help keep supplies off the floor, protecting them from moisture and pests. Prioritize easy access to frequently used items to speed up workflow and avoid clutter buildup. Regularly review your storage areas to discard obsolete or damaged materials, maintaining order and freeing valuable space. With a strategic approach to storage solutions and material organization, you gain control over your workspace, enhancing both safety and efficiency, and ultimately securing the freedom to focus on your craft.
Preventative Maintenance for Machinery and Equipment
A proactive approach to preventative maintenance keeps your machinery running smoothly and prevents costly downtime. Regular machinery lubrication reduces friction, extending equipment life. Frequent equipment inspection helps you catch issues early before they escalate. Stick to a maintenance schedule to guarantee no step is overlooked.
Here’s a checklist to keep you on track:
- Perform daily machinery lubrication on all moving parts.
- Conduct weekly equipment inspections to identify wear or damage.
- Replace worn components promptly to avoid breakdowns.
- Keep maintenance logs to track servicing and repairs.
Best Practices for Ventilation and Air Quality Control
Although maintaining clean machinery is essential, ensuring proper ventilation and air quality is equally important to protect both your wood products and your workforce. You should install efficient air filtration systems to capture dust and airborne particles, reducing health risks and preventing contamination of wood surfaces. Regularly inspect and replace filters to maintain peak performance. Humidity control is critical; excessive moisture can warp wood, while low humidity causes cracking. Use dehumidifiers or humidifiers to keep levels stable between 40-60%. Proper airflow circulation helps dissipate fumes and dust, so incorporate exhaust fans and strategically placed vents. Monitoring air quality with sensors allows you to respond promptly to any issues. By prioritizing ventilation and air quality control, you safeguard your products’ integrity and create a safer, more productive workspace.
Häufig gestellte Fragen
How Often Should Professional Wood Shops Schedule Full Facility Cleanings?
Think of your wood shop like a finely tuned guitar; if you don’t tune it regularly, the sound suffers. You should schedule full facility cleanings at least monthly deep cleanings to keep dust and debris from dulling your tools and workspace. Pair these with seasonal maintenance schedules to address more extensive upkeep. This routine not only extends your equipment’s life but also frees you to focus on crafting, not fixing.
What Eco-Friendly Cleaning Products Are Safe for Wood Shop Use?
You’ll want to choose natural cleaners that are tough on dirt but gentle on your wood surfaces. Biodegradable options, like vinegar-based solutions or plant-derived soaps, effectively break down grime without harmful chemicals. These products reduce environmental impact and guarantee your workspace stays safe for you and your team. Avoid harsh solvents that can damage wood finishes. By opting for eco-friendly cleaners, you maintain quality while embracing a sustainable, responsible approach in your shop.
Can Cleaning Routines Affect the Longevity of Wood Finishes?
Absolutely, your cleaning routines play an essential role in wood finish maintenance. If you clean too frequently or use harsh products, you risk wearing down the finish prematurely. Conversely, neglecting cleaning can allow dirt and grime to degrade the surface. Finding the right cleaning frequency effects balance guarantees your wood finishes stay protected and vibrant longer. Stick to gentle, appropriate methods to preserve both the beauty and durability of your wood surfaces.
How to Train New Employees on Cleaning Protocols Effectively?
To train new employees effectively, you’ll want to combine hands-on demonstrations with clear written guidelines. Show them the exact cleaning techniques in action, so they can observe and practice immediately. Provide written instructions they can reference anytime, ensuring consistency and independence. This approach empowers them to master protocols confidently and maintain high standards without constant supervision, giving you peace of mind while they work freely and responsibly.
What Are Common Cleaning Mistakes in Wood Businesses to Avoid?
You’ll want to avoid dust accumulation, which can damage wood surfaces and create health hazards. Don’t let dust settle by skipping regular cleaning or using improper tools. Also, chemical misuse is a common error—using harsh cleaners can ruin finishes or cause safety issues. Stick to recommended products and dilution ratios. Being detail-oriented with these practices guarantees your workspace stays clean and your freedom to work effectively remains intact.