Daily Maintenance Tips for Grease
You should inspect grease points daily to catch wear and contamination early, using tailored checklists for consistency. Always apply the correct grease type and clean fittings before each application to prevent damage. Avoid over-greasing by following manufacturer guidelines and monitor grease temperatures to spot overheating. Store grease properly to avoid contamination, and make sure your team is trained on proper handling techniques. Keeping these routines sharp will help you maintain peak equipment performance—there’s more to master for ideal results.
Inspect Grease Points Regularly
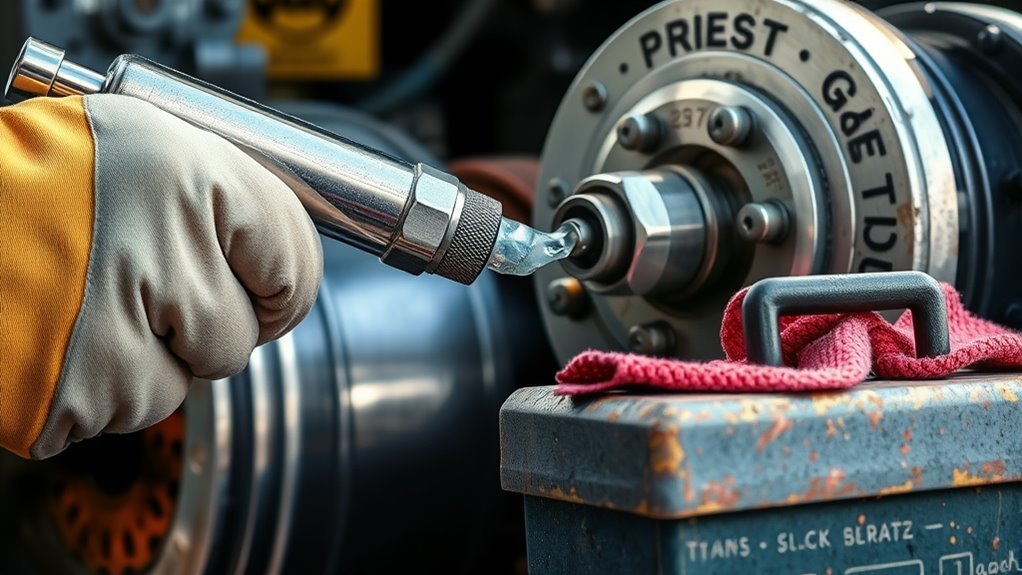
Regularly inspecting grease points is essential to keep your equipment running smoothly and prevent costly breakdowns. You need to integrate regular inspections into your lubrication schedules to identify wear, contamination, or insufficient grease early. Pay close attention to joints, bearings, and fittings where grease accumulates or depletes quickly. By following a strict inspection routine, you’ll catch problems before they escalate, ensuring your machinery remains reliable. Skipping these checks risks equipment failure, limiting your operational freedom. Use checklists tailored to your equipment to streamline the process and maintain consistency. Staying disciplined with these inspections maximizes performance and extends equipment life, giving you the control and independence you want without unexpected downtime.
Use the Correct Type of Grease
You need to choose grease that’s compatible with your equipment to avoid damage and guarantee peak performance. Consider the operating temperature and select a grease with the right viscosity to maintain proper lubrication under those conditions. Using the correct type prevents breakdowns and extends the life of your machinery.
Grease Compatibility Matters
Although it might seem convenient to mix different greases, doing so can compromise your equipment’s performance and lifespan. Different grease types often have incompatible base oils and thickeners, leading to separation, reduced lubrication, or even corrosion. To maintain freedom from unexpected breakdowns, always perform compatibility testing before switching or combining greases. This testing guarantees the greases will work together without adverse effects. Using the correct, compatible grease type extends equipment life and optimizes operation. Don’t gamble with your machinery by ignoring compatibility—it’s a critical step in daily maintenance that safeguards your investment and keeps you in control. Prioritize compatibility to avoid costly repairs and downtime, keeping your equipment running smoothly and efficiently at all times.
Temperature and Viscosity
Selecting the right grease goes beyond compatibility; temperature and viscosity play a major role in effective lubrication. You need to understand how temperature effects cause viscosity changes, impacting grease performance and equipment freedom.
Keep these three points in mind:
- High temperatures thin grease, reducing its viscosity and protection.
- Low temperatures thicken grease, increasing resistance and wear.
- Choose grease formulated for your operating temperature range to maintain ideal viscosity.
Clean Grease Fittings Before Application
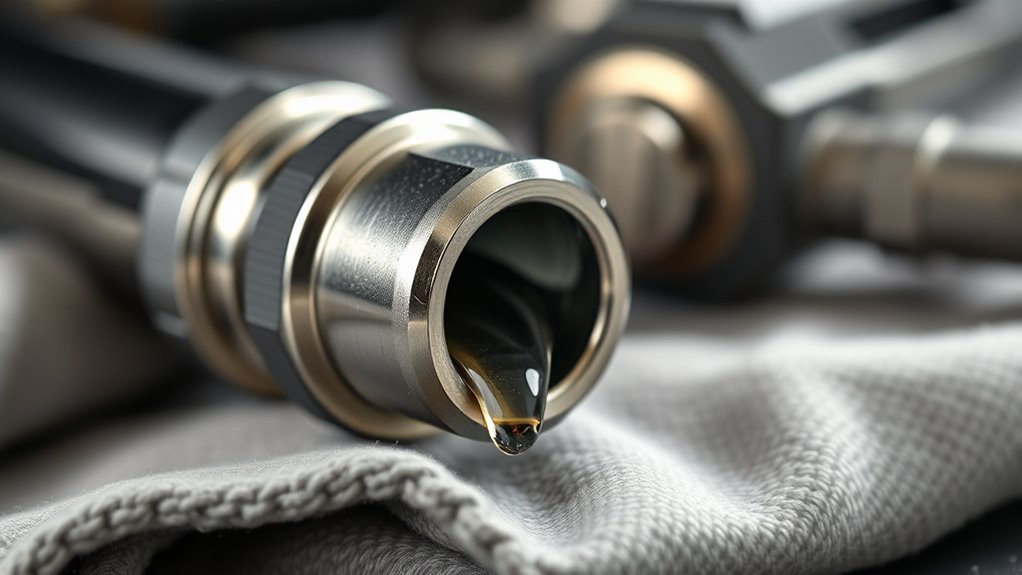
Before applying grease, always clean the fittings thoroughly to prevent contaminants from entering the lubrication system. Use effective cleaning techniques such as wiping fittings with a lint-free cloth or using a solvent-soaked brush to remove dirt and old grease. This step is vital for fitting maintenance, ensuring smooth grease flow and avoiding premature wear or failure. Neglecting this process risks introducing abrasive particles that compromise machinery performance. By consistently cleaning grease fittings before application, you maintain system integrity and extend equipment lifespan. Remember, proper fitting maintenance isn’t optional—it’s essential for reliable operation and your freedom from unnecessary repairs. Stay disciplined with cleaning techniques to safeguard your equipment and keep your operations running smoothly every day.
Avoid Over-Greasing Machinery
When you apply grease, it’s crucial not to overdo it. Over-greasing can lead to increased friction, seals bursting, and contamination of components, ultimately shortening your machinery lifespan. To keep your equipment running freely and efficiently, follow these key steps:
- Apply grease sparingly according to manufacturer guidelines—excess won’t improve performance.
- Use a grease gun with a pressure gauge to control the amount precisely.
- Inspect grease fittings regularly to verify they’re not blocked or damaged, which can cause improper grease distribution.
Monitor Grease Temperature Levels
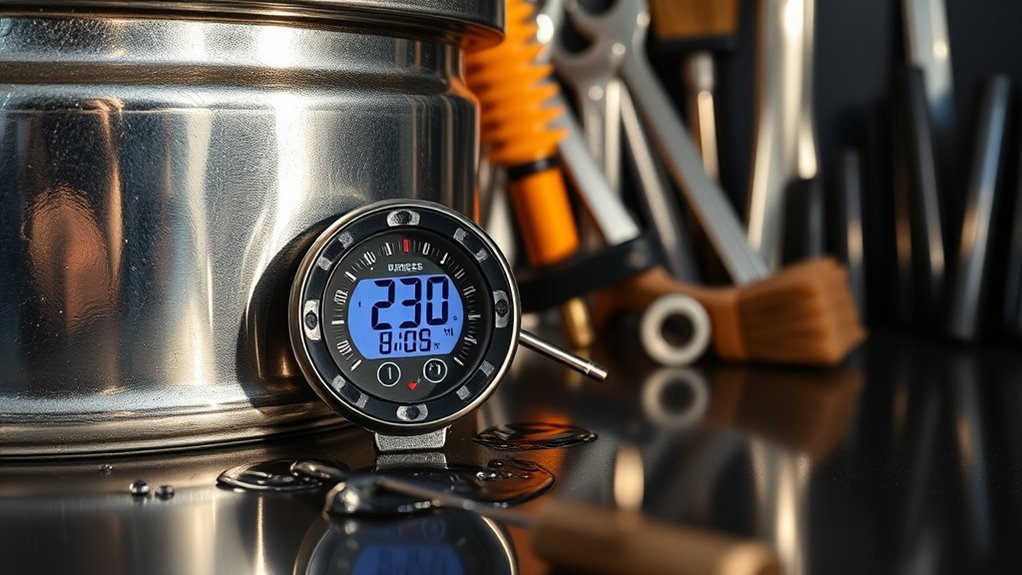
You need to keep grease within its ideal temperature range to guarantee peak performance and prevent damage. Use temperature monitoring tools regularly to catch any overheating early. Remember, excessive heat can break down grease, reducing its effectiveness and risking machinery failure.
Ideal Temperature Range
Although grease can perform well in various conditions, maintaining it within the ideal temperature range is essential to guarantee its effectiveness and longevity. Temperature effects directly impact grease performance, so you need to keep it stable. Here’s what you should consider:
- Low Temperatures: If grease gets too cold, it thickens, reducing flow and causing poor lubrication.
- Optimal Range: Most greases perform best between 40°F and 120°F (4°C to 49°C), balancing viscosity and protection.
- High Temperatures: Excessive heat breaks down grease, leading to oxidation, hardening, and loss of lubricating properties.
Temperature Monitoring Tools
Since maintaining grease within the ideal temperature range is crucial, using reliable temperature monitoring tools becomes essential for effective lubrication management. You’ll want to install accurate temperature sensors directly on or near grease-lubricated components to continuously track heat levels. These sensors feed real-time data into monitoring systems, allowing you to detect temperature deviations quickly and take corrective action before damage occurs. Modern monitoring systems often offer alerts and detailed analytics, empowering you to optimize maintenance schedules and extend equipment life. By relying on precise temperature sensors and integrated monitoring systems, you maintain control over grease condition effortlessly, ensuring performance and preventing costly failures. Embracing these tools lets you keep your operations running smoothly without unnecessary interruptions or guesswork.
Effects of Overheating
When grease temperature rises beyond recommended levels, its lubricating properties degrade rapidly, leading to equipment damage and reduced operational efficiency. You need to watch for overheating signs to prevent costly machinery damage. Here’s what you should monitor closely:
- Increased friction noise or vibration – a clear indication grease is no longer protecting moving parts effectively.
- Discoloration or odor changes – these signal chemical breakdown from excessive heat.
- Grease consistency thinning – overheating causes grease to lose its structure, impairing lubrication.
Store Grease Properly to Prevent Contamination
To keep grease effective and extend its lifespan, you need to store it in a clean, dry environment away from contaminants like dirt, dust, and moisture. Proper storage is essential for contamination prevention, ensuring the grease maintains its consistency and performance. Always seal containers tightly after use to block out air and debris. Use dedicated, clean tools when handling grease to avoid introducing foreign particles. Store grease off the floor, ideally on shelves or pallets, to reduce exposure to moisture and dirt. Keep storage areas organized and away from chemicals or extreme temperatures that could degrade the grease. By implementing these straightforward practices, you maintain grease quality, protect your equipment, and preserve your freedom from unnecessary maintenance issues caused by contaminated lubricant.
Train Staff on Proper Grease Handling Techniques
Anyone handling grease must be properly trained to guarantee correct application and avoid contamination. Prioritizing grease safety means mastering handling procedures that protect both product integrity and your equipment’s performance. To verify your team is up to speed, focus on these key training points:
- Correct Application Methods: Teach precise grease amounts and tools to prevent overuse or contamination.
- Personal Protective Equipment (PPE): Emphasize gloves, goggles, and clean uniforms to maintain cleanliness and safety.
- Storage and Disposal: Instruct on proper sealing, storage temperatures, and disposing of used grease safely.
Frequently Asked Questions
How Often Should Grease Be Replaced Entirely in Machinery?
You should base the grease replacement frequency on the grease lifespan specified by your machinery’s manufacturer. Typically, grease needs full replacement every 6 to 12 months, but heavy-duty or high-temperature environments might shorten that. Don’t just guess—monitor for contamination or breakdown signs. Staying proactive with grease replacement frequency guarantees your equipment runs smoothly and freely without unexpected downtime. Keep records to optimize maintenance schedules and extend machinery life.
Can Mixing Different Grease Brands Cause Damage?
Did you know that 30% of machinery failures stem from improper lubrication? When mixing different grease brands, you risk compromising grease compatibility due to varying brand formulations. This can cause thickening, separation, or reduced lubrication, ultimately damaging your equipment. To keep your machinery running smoothly, always check the grease specifications and avoid mixing unless the products are confirmed compatible. Protect your freedom to operate without costly downtime by sticking to one trusted grease type.
What Are the Signs of Grease Failure in Equipment?
You’ll notice grease failure when you see grease leaks around seals or joints, signaling that lubrication isn’t holding up. Equipment wear is another clear sign—if parts are grinding, overheating, or showing unusual noise, the grease might be breaking down. Don’t ignore these symptoms; they restrict your equipment’s freedom to operate smoothly. Catching these signs early helps you act fast, preventing costly downtime and extending your machinery’s life.
Is Synthetic Grease Better Than Conventional Grease?
Did you know synthetic grease can last up to three times longer than conventional grease? If you want to maximize grease longevity, synthetic advantages are clear—it resists breakdown under extreme temperatures and heavy loads. By choosing synthetic, you’re reducing maintenance frequency and downtime, freeing yourself from constant equipment worries. Its superior stability and performance give you more control and reliability, making it a practical choice for anyone seeking durable, hassle-free lubrication.
How Does Humidity Affect Grease Performance?
Humidity can seriously impact grease performance by affecting its viscosity and moisture absorption. When moisture gets into the grease, it can thin out the grease viscosity, reducing its ability to lubricate effectively. This means your equipment might face increased wear or corrosion. To keep your machinery running smoothly and maintain your freedom from breakdowns, choose grease formulated to resist moisture absorption, especially if you operate in humid environments.